Intel Patent Brings AI Robot Coworkers to Factory Floors
Intel’s latest patent shows that it wants robots to co-work with humans — without the risk of hurting them.
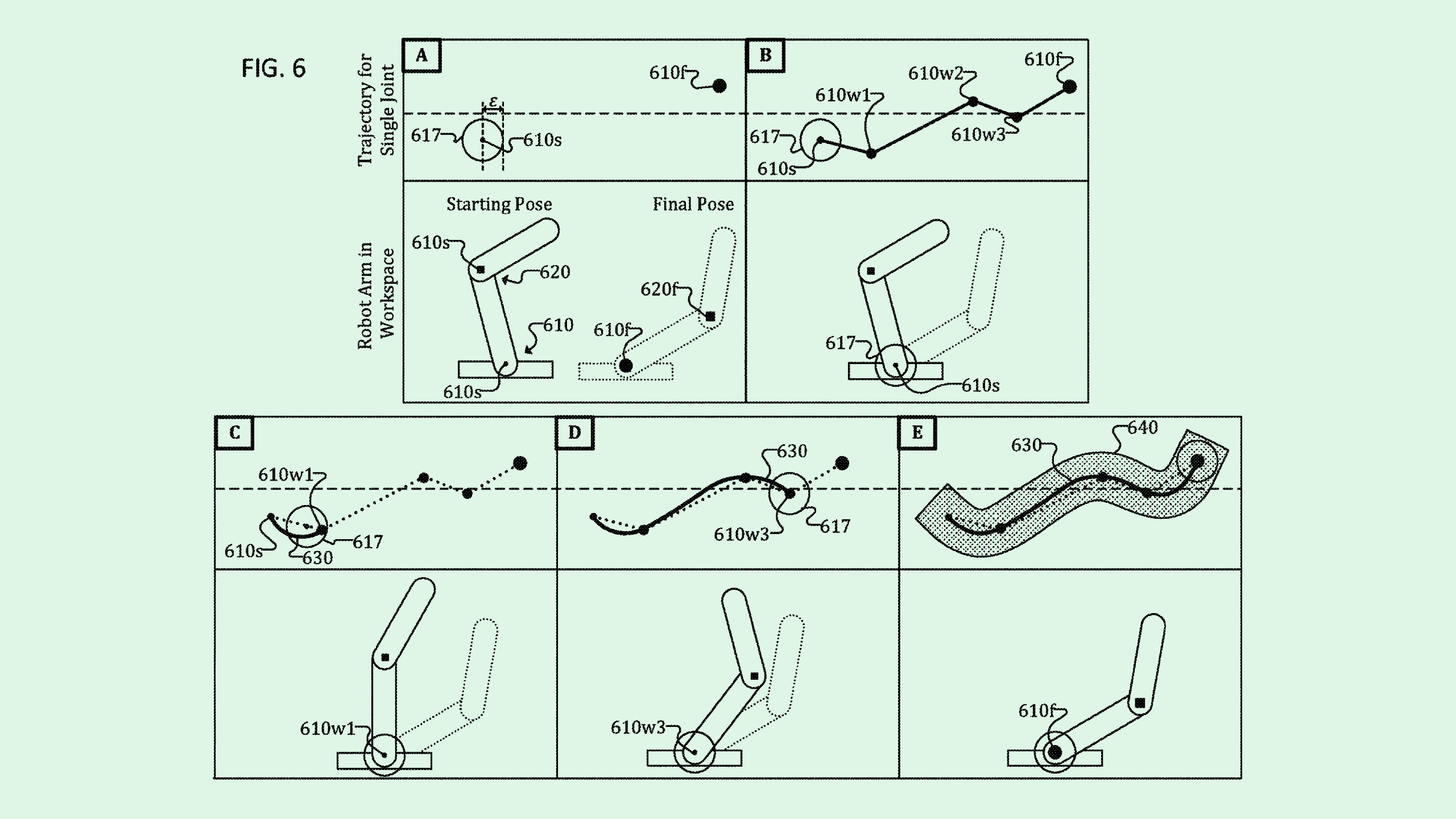
Sign up to uncover the latest in emerging technology.
Intel wants to make sure its robots don’t trip people up.
The tech firm is seeking to patent a “real-time motion and path planner” for robots. Intel’s patent details a system that helps autonomous robots move in accordance with their surroundings using sensor data and a building’s “occupancy information,” meaning who and what are around it.
“As the number of robots in such environments increases, so does the risk of hazardous interactions among robots and humans in shared spaces,” Intel noted in the filing. “Due to their size and cost … the processing and memory requirements for motion planning may be limited.”
Intel’s system plans around occupancy information in real time by calculating “occupancy probability” to determine whether the immediate space around the robot will be occupied or free. This uses a host of different sensors such as infrared cameras, depth and motion sensors, and LiDAR.
This occupancy information is then used to track a series of “collision-free waypoints” in between its starting state and its task goal using continuous scans of this sensor data. If the environment surrounding the robot becomes occupied, an “actions handler” within the system will re-plan the robot’s course of action.
Intel noted that this system may be put to use in structures such as a “manufacturing floor, an office building, (or) a warehouse,” such as a packaging robot in a shipping facility, a manufacturing robot in a factory, or a security robot in an office.
Conventional environmental monitoring and motion planning systems tend to map out the entirety of a space over a 3D grid, then plan out a robot’s trajectory from start to finish. However, in this case a robot may see too many spaces as being occupied, leading to it “overly restricting the movements of the robot.” By only monitoring the space directly around it, Intel’s system overcomes that issue, while also saving on computational resources.
Though Intel’s filing aims to improve the range of movement by robots in a factory setting, something that seems to be missing from this patent is what happens in the event of a collision, said Rhonda Dibachi, CEO of Manufacturing-as-a-Service platform HeyScottie. It’s safest for robots in manufacturing and logistics settings to have a “kill switch,” she said, because accidents can happen no matter how intelligent a machine is.
As it stands, there are strict regulations from the American National Standards Institute regarding how robots can be used in factory settings, Dibachi said, often limiting these machines’ capacity by keeping them fenced off from human interaction while in operation. But making these machines as safe as possible is a critical part of allowing them to coexist with human workers more efficiently, she said.
“To allow robots to integrate with humans is the next big thing,” said Dibachi. “If a worker has a robot buddy, they’re going to be much more effective. But if there’s any possibility that a robot is going to be able to harm somebody, it can’t coexist.”
While Intel’s patent references how this tech could be useful in collaboration with human occupants of a space, it also notes that this tech is “not limited to strictly human collaborations,” and could be applied to any “dynamic objects” it may share a space with. To that end, a patent like this could be helpful in bringing production closer to a lights-out model, in which there’s little to no human involvement.
And with 2.1 million unfulfilled manufacturing jobs expected 2030 according to the Manufacturing Institute, decreasing reliance on human labor may be a crucial stopgap to an impending labor shortage.